Iowa’s second mass timber project underway in Valley Junction
The mixed-use project will include 11 apartment units
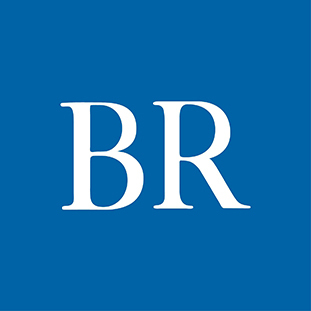
KATHY A. BOLTEN Jul 27, 2022 | 7:30 pm
5 min read time
1,294 wordsBusiness Record Insider, Real Estate and Development
Des Moines-area builder Peter Cutler was cautious yet excited when his brother, a developer, approached him about using mass timber to construct a mixed-use project in West Des Moines’ Valley Junction.
“I anticipated it to be very challenging,” said Peter Cutler, owner of Cutler Construction, based in Waukee. “What surprised me the most was that everything fit well.”
Several different suppliers and designers were part of the project at 304 Fifth St. in West Des Moines, Cutler said. A structural engineer and architect also worked on the project, a three-story, 13,617-square-foot building that includes commercial, office and 11 apartment units.
“We have all of these different products coming from different places. … It just seemed like a recipe for something going wrong,” Cutler said. “But, lo and behold, it all has gone together very easily.”
Scott Cutler, who founded Cutler Development in 2017, was well into planning the Valley Junction project when architect Daniel Willrich suggested Cutler consider using mass timber in the building.
Willrich, director of architecture/business development for Pelds Design Services in Des Moines, had attended a national convention where he heard several speakers praise the benefits of using mass timber in projects instead of steel and traditional stick lumber.
He shared what he had learned with Scott Cutler.
“The speakers talked a lot about why it’s a good building material not only for the aesthetics it brings to a project but environmental sustainability that’s inherent in it,” Willrich said. “We dug into it a little more and [Scott] decided to redesign the project with mass timber.”
Before Cutler made a final decision on whether to use the material in the mixed-use project, he and wife Molly Cutler drove to Oregon to visit the family-owned sawmill that produces the product.
Freres Engineered Wood is a “very innovative company and jumped out in front of the pack to develop this type of mass timber,” said Molly Cutler, a manager at Cutler Development. “This particular type of mass timber has a lot less waste of the wood, and you can actually calculate how much carbon is getting sequestered.”
When they returned from the trip, the green light was given to use mass timber in the project.
“The change in appearance was just aesthetic,” Willrich said. “But it was a full redesign for our structural engineer.”
What is mass timber?
Mass timber is a new category of wood product that consists of multiple layers of young timber that are nailed or glued together. The compressed wood forms structurally sound and load-bearing material that can be panelized – built in a factory rather than on-site – for construction. The finished product is strong but more lightweight than concrete or steel columns, beams or panels.
Buildings up to 18 stories tall can now be built with mass timber after changes to the International Building Code went into effect in 2021.
The use of mass timber products can be more cost- and time-efficient than steel, concrete or traditional lumber products, Willrich and Scott Cutler said. Much of the lumber used in the building under construction in Valley Junction was prefabricated off-site, they said.
“The building tends to go up faster because the pieces are milled to exact specifications,” Willrich said. “It’s like a big puzzle. It goes up quicker because it’s lighter than moving steel around and it takes fewer people to get the work done.”
The project is Iowa’s second mass timber development and the first one to include a residential component, Scott Cutler said. The state’s first mass timber project is located at 111 E. Grand Ave. in Des Moines’ East Village neighborhood.
Environmentally friendly
One of the main reasons Scott and Molly Cutler have become mass-timber fans is the product’s environmental benefits, they said.
Steel and concrete are responsible for much of the construction industry’s carbon emissions, according to Architecture 2030, a Santa Fe, N.M., nonprofit group established 20 years ago in response to climate-related issues. Human-made structures including buildings, roads and utility-related structures account for 50% of carbon dioxide emissions, 20% of which comes from building materials and construction, according to the group.
The use of wood materials made from trees sequesters or captures carbon by taking it out of the atmosphere.
In addition, the Oregon-based company that supplied much of the mass timber for the building at 304 Fifth St. harvests trees that are 5 to 10 years old and replaces them with newly planted trees, Molly Cutler said. “They are not cutting down old-growth, giant, beautiful trees. And by replanting new trees almost immediately, there’s an ongoing sustainability factor.”
In traditional lumber production, two-by-fours and other lumber pieces are cut out of the circular tree trunks, “leaving behind a lot of waste,” Molly Cutler said. “At the Oregon company, they use technology that basically peels the tree back in layers, which leaves next to no waste – another environmental benefit – and produces a beautiful, repeating knot pattern.”
Not all of the wood in the Valley Junction project is mass timber, Scott Cutler said. Much of the interior framing was built with traditional wood studs. “This project is more of a hybrid mass timber project,” he said.
The Valley Junction development was the first Iowa project to be awarded a U.S. Forest Service’s Wood Innovations Grant, receiving $243,035 in 2021.
A building permit valued at $1.8 million was issued for the project in August 2021. Construction is expected to be completed by December.
Scott Cutler bought the property in January 2021, which included a two-story house that was razed.
Cutler said he’ll likely use mass timber products in future development projects.
“We are excited about this project and hope we can share our learnings and knowledge with others to help them better understand the benefits of mass timber,” he said.
Restaurant, DSM Culinary tenants in new building
Street-level space of a building under construction in West Des Moines’ Valley Junction will be occupied by a restaurant operated by Ryan Cooper and by DSM Culinary, which offers a variety of cooking classes to the public.
Both have received grants from a city of West Des Moines program supporting commercial redevelopment in Valley Junction.
Cooper, whose new restaurant will offer steaks, pasta dishes and pizza, said the mass timber building under construction at 304 Fifth St. “is getting a lot of attention and recognition” because of the materials being used to construct it.
“The space is gorgeous,” he said. “I kind of half joke that I wanted to take that space as much to get it for myself as to not let someone else have it … because it’s such a very attractive spot.”
Cooper, who owns and operates Cooper’s on 5th and Winchester Public House, both along Valley Junction’s Fifth Street, said the yet-to-be named new restaurant “will have a slight Italian vibe to it.”
Developer Scott Cutler owns the buildings Cooper’s other two Valley Junction businesses are located in. “When [Cutler] showed me the building, everything just clicked,” said Cooper, who was awarded $37,500 from the West Des Moines grant program.
Cooper, who has partners in the new business venture, said he expects the restaurant to open in mid-2023.
Cass Spence currently operates DSM Culinary out of space in Des Moines’ East Village. She said she had been looking for a new place in which to operate her business for the past three years.
“This opportunity came up. … When I got the opportunity to walk through the building, I was really impressed with it,” Spence said. DSM Culinary was awarded $16,402 from the West Des Moines program.
Spence said she hopes to begin offering culinary classes in the new space later this year or in early 2023. In addition to the classes, Spence makes and sells dumplings.