Tyson closure reflects the tight labor market
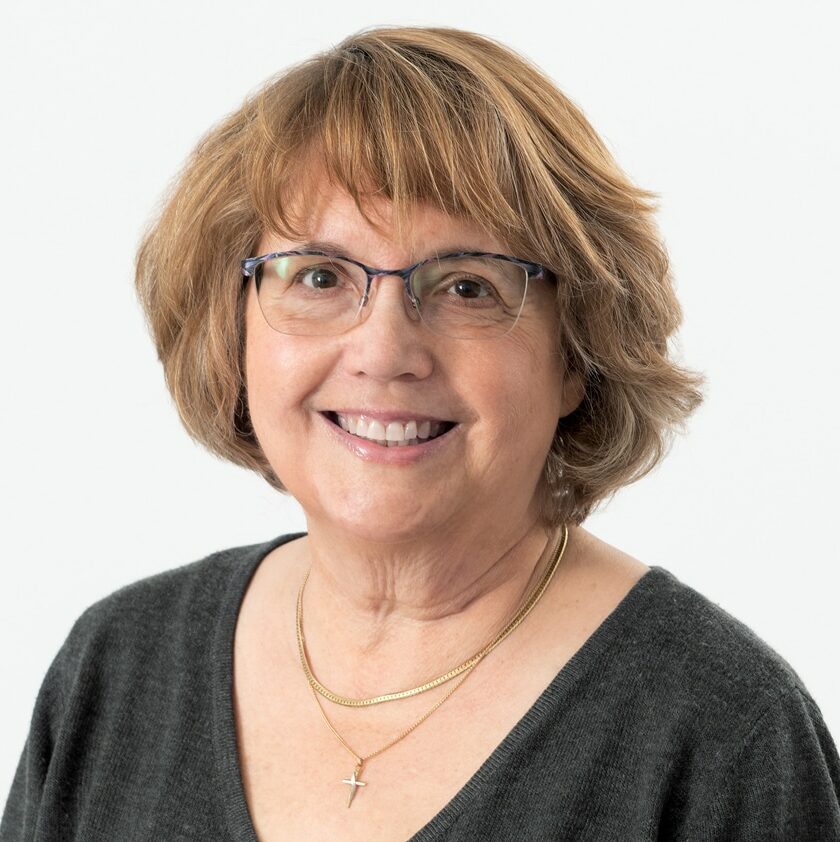
In spring 2018, Tyson Fresh Meats Inc. requested the state of Iowa’s help with financing a $43.7 million project to modernize the company’s decades-old processing plant in Perry.
The approved request was expected to provide Tyson with over $670,000 in tax credits. Over the next five years, Tyson made improvements to the Perry plant, but it ended up declining the state incentives because it couldn’t meet hiring requirements.
“There have been struggles to get enough applicants to fill all positions,” a Tyson official wrote in a letter to the Iowa Economic Development Authority board in mid-2021.
In March, the Arkansas-based meat producer announced the Perry plant will be permanently closed on June 28, a move that will leave nearly 1,300 people jobless. Tyson is Perry’s largest employer and operates a plant that has been in the community for over 60 years.
Tyson officials are mum about what prompted the decision to close the plant and did not respond to interview requests. Observers have speculated that the pork industry’s financial struggles in the past year – rising processing costs that have outpaced prices paid to hog producers – played a part in Tyson’s decision to close the plant. Others have wondered whether the presence of a union at the Tyson plant played a role in the decision to close the facility.
But there are also questions about whether the ability to attract and keep workers contributed to the move to shutter the plant. Industry watchers have said Tyson wanted to start a second shift at the Perry plant but couldn’t find enough workers.
“I think it may have come down to where they were going to put their resources in a tight labor market,” said Sven Peterson, Perry’s city administrator.
Officials with the state of Iowa and in Perry are hopeful history will repeat itself and the community will be able to find a different company to occupy the Perry plant. In 1988, after Oscar Mayer Corp., which occupied the Perry facility for over 20 years, announced it was shuttering the plant, Iowa Beef Processors stepped forward and bought the facility. Questions exist, though, whether Iowa’s tight labor market will hinder a new buyer for the plant.
“In Iowa, it’s a very tight labor market and there’s just not enough workers for the number of jobs that there are,” said Ben Ayers, a senior economist with Nationwide. “It’s hard to make a hire if you can’t find a worker.”
Attracting and retaining workers is not a new issue in Perry, Peterson said. Over a year ago, the city of Perry held a roundtable discussion with employers about issues they faced, he said.
“Being able to attract a workforce was the top concern,” Peterson said. The need was not industry-specific, nor is it unique to Perry, he said. “It’s a statewide issue that everyone is facing.”
The inadequate supply of hourly workers was cited by Iowa manufacturing companies as the top inhibitor to growth in the 2023-24 biennial assessment of manufacturers by Iowa State University’s Center for Industrial Research and Service (CIRAS). It was the first time that a lack of workforce was listed as manufacturers’ top issue, said Michael O’Donnell, CIRAS’ director.
In recent follow-up conversations with leaders of manufacturing companies, the ability to find workers has improved slightly, but not much, O’Donnell said. “In reality, we don’t see it getting any better for a pretty long time.”
In February, Iowa had 1,700,900 people in its labor force, 26,000 fewer than in February 2020, Iowa Workforce Development data shows. Iowa, with an unemployment rate of 2.9%, has nearly 61,000 job openings posted on the agency’s website.
An aging population is among the reasons for the decline in Iowa’s workforce, Ayers said. And there are not enough young people either moving into Iowa or staying in the state after graduating from high school or college to replace those who are retiring, he said.
Companies in Iowa unable to find workers will either opt to not move forward with expansions or relocate to areas of the country where workers are plentiful, Ayers said.
Companies looking to open new facilities may bypass Iowa altogether, he said. “It’s not surprising that a lot of companies, especially tech companies, are rushing to Arizona, a place where they can find workers and where universities are pumping out graduates.”
Touting the benefits of living in Iowa, including its low cost of living and housing affordability is one way the state can attract and retain workers, Ayers said. “Highlighting those benefits that are innate to the area can draw in workers, especially if they understand that they can have good lives and good careers [in Iowa].”
Lack of an adequate supply of housing is also an issue facing Iowa, which is projected to need nearly 25,000 new residences by 2030. Owner-occupied homes account for 70% of the new housing needed in Iowa’s rural, suburban and urban areas, according to a recent state report.
Perry officials understand the connection between supplying businesses with a workforce and the need for an adequate supply of housing, Peterson said. Between 2010 and 2016, no new homes were built in Perry, prompting the city to adopt a tax abatement program, he said. Since 2016, 60 new homes and 60 apartment units have been built in the community of over 8,000 people.
“We’ve made some decent strides in that arena but still, when you’re talking about hundreds of employees and you only get a handful of new units a year – it will take a while to catch up,” Peterson said.
The struggle to provide housing for workers is not unique to Perry. In Osceola, where Osceola Food is located, workers frequently cite housing as a factor in deciding whether to work at the plant, Miguel Aparicio, human resources manager at the facility, wrote in an email.
“Currently, some families are staying in extended-stay motels until permanent housing becomes available,” he wrote. “For those who cannot find suitable housing locally, commuting from nearby areas is often the alternative.”
Some companies are helping pay for new housing in the communities in which they are located. In 2022, JBS Food Group, which operates three pork processing plants in Iowa, provided $1.2 million toward the development of a three-building apartment project in Ottumwa. The development included 108 apartment units, 85% of which included two bedrooms. The remainder were three-bedroom units. A similar investment was made in 2023 in Marshalltown, where a 103-unit complex was built.
Nearly all of the units in both complexes are occupied by JBS workers.
“We are working to make the local Iowa communities we call home, thrive,” Matthew Connelly, a spokesperson for Colorado-based JBS, wrote in an email.
JBS and Osceola Food also provide tuition assistance programs to employees and their children.
Companies that understand “what their employees’ biggest issues and challenges are and then do the things that make [the employees’] lives better are the ones that will also attract and keep workers and at the same time, grow the business,” CIRAS’ O’Donnell said.
Timeline: A history of meatpacking in Perry
The city of Perry’s ties to the meat processing industry date back to the mid-1800s, when the community had several small butcher shops that served surrounding hog farmers. After Gustavus Swift, founder of Swift & Co., invented the refrigerated railcar around 1877, the meatpacking industry quickly grew. Instead of putting live livestock on railcars, animals were butchered and meat transported in refrigerated railcars. The regional rail lines that served Perry provided a way for butchers to transport meats to larger communities in Iowa and surrounding states. The following is a history of meatpacking in Perry, compiled from information submitted to the National Register of Historic Places, a capstone report for the Iowa Certified Public Manager program and the Perry News.
1919 – Charles Hausserman, who operated a meat market in Perry, starts a packing plant that was operational by June 1920. It employed 34 people.
1926 – Hausserman Packing Co. closes in the mid-1920s because of issues related to an improperly built cold storage area. The plant reopens in 1926 as the Perry Packing Co.
1936 – Perry Packing Co. is sold to Swift & Co., headquartered in Fort Worth, Texas.
1956 – The Perry plant closes because of issues related to water and sewer.
1960 – Perry Industries begins construction on a new meatpacking facility just west of the community.
1962 – The new plant opens under the name Iowa Pork Producers.
1963 – Iowa Pork merges with Iowa Beef Processors, which continues to operate the plant.
1965 – Oscar Mayer Corp. buys the plant and starts production with 350 full-time workers. By 1975, the plant had 750 employees, nearly all white males.
1980s – The meatpacking industry, plagued by falling demand for meat and other economic woes, begins renegotiating union contracts, closing plants and reopening them as nonunion workplaces, and permanently shuttering plants. In
1983, the average base hourly wage of workers at meatpacking plants was cut from $10.69 to $8.19.
1988 – Oscar Mayer Corp. announces the Perry plant will close in 1989, affecting about 800 people, or 20% of Perry’s workforce.
December 1988 – Iowa Beef Processors announces it will buy the plant and remodel it as a kill and boning facility. Production was slated to start in the summer of 1989. IBP did not recognize the union. Starting wages were $5.80 an hour. Few people who had worked for Oscar Mayer remained at the plant. Some former workers transferred to Oscar Mayer plants in other parts of the U.S.; others received tuition assistance to go to college, learned a new trade or skill or found jobs in other communities or companies.
1989 – IBP recruits people from Texas, California, Mexico and Central America to work at the Perry plant. By 1992, about 40% of IBP’s workforce was Latino.
2001 – Tyson Fresh Meats acquires the plant, after buying IBP Inc.
March 2024 – Tyson announces plant will close in June.
Osceola Food faces challenges in attracting, keeping workers
The Business Record recently reached out to Osceola Food about the meat processing company’s ability to attract and retain employees. Hormel Foods, which operates Osceola Food, opened the plant in 1996. The company’s Iowa subsidiary employs 680 people. In late March, it listed more than two dozen job openings with pay that ranged from $19 an hour to $81,000 per year. The company responded to questions via email.
Answers have been edited for brevity and clarity.
How long does it take to fill open positions at Osceola Food?
Miguel Aparicio, manager, human resources, Osceola Food: “For production food worker positions, the average time to fill vacancies typically ranges from a couple weeks to a month. However, this can vary based on factors such as the volume of applicants, the urgency to fill the position and any specific skill requirements.”
Are certain jobs easier to fill than others?
Aparicio: “Yes, certain jobs tend to be easier to fill than others due to factors such as the shift, department, required qualifications and skills. Entry-level positions like production line workers or general laborers may be easier to fill compared to specialized roles requiring specific skills or experience, such as smokehouse techs, maintenance mechanics or quality control auditors.”
How does worker turnover at Osceola Food compare with turnover at other Hormel plants?
Aparicio: “We’ve found that our worker turnover rates are similar to those at other Hormel plants. However, there’s a unique aspect to consider: our location. We are about 45 miles away from a major metro area. We face some challenges in attracting and retaining talent compared to plants located closer to urban places. This geographical factor plays a significant role in our turnover rates, as it affects the size and diversity of our candidate pool.”
From where does Osceola Food typically draw its employees?
Aparicio: “While a portion of our workforce comes from Osceola itself, we also draw employees from surrounding areas and communities within Iowa. Additionally, we attract talent from the Des Moines area and other nearby regions. … We are the largest employer in Osceola.”
How does the ability to find workers to fill jobs in Iowa compare to other areas where Hormel has facilities?
Aparicio: “Generally, Iowa offers a diverse workforce with individuals possessing a range of skills and experiences. Like many rural areas, attracting and retaining workers in smaller communities can present challenges compared to larger metropolitan areas where there may be a larger pool of candidates.”
What incentives does Osceola Food offer to attract and retain workers? Some job listings note college tuition for a two-year degree offered as an incentive.
Amy Sheehan, director of talent acquisition, human resources, Hormel Foods: “The Hormel Inspired Pathways program was created to help make the dream of a college education a reality for the children of [Hormel Foods] team members. The program provides a full range of educational services … including tuition for two-year community college degrees, individual college advising, support navigating the financial aid system, assistance with transferring to or planning for [a] four-year college degree.”
Hormel Foods has spent nearly $1 million to send over 450 children of Hormel Foods employees to 76 unique community colleges. Forty of the students that have or are participating in the program are from Osceola.
The company also offers an employee tuition assistance program.
Has Osceola Food reached out to Tyson workers who will be displaced by the plant closing in Perry?
Aparicio: Representatives of Osceola Food have been [in] Perry to “spread the word that we are hiring at Osceola Food. We believe in supporting the local community and providing opportunities for those affected by the plant closure.”
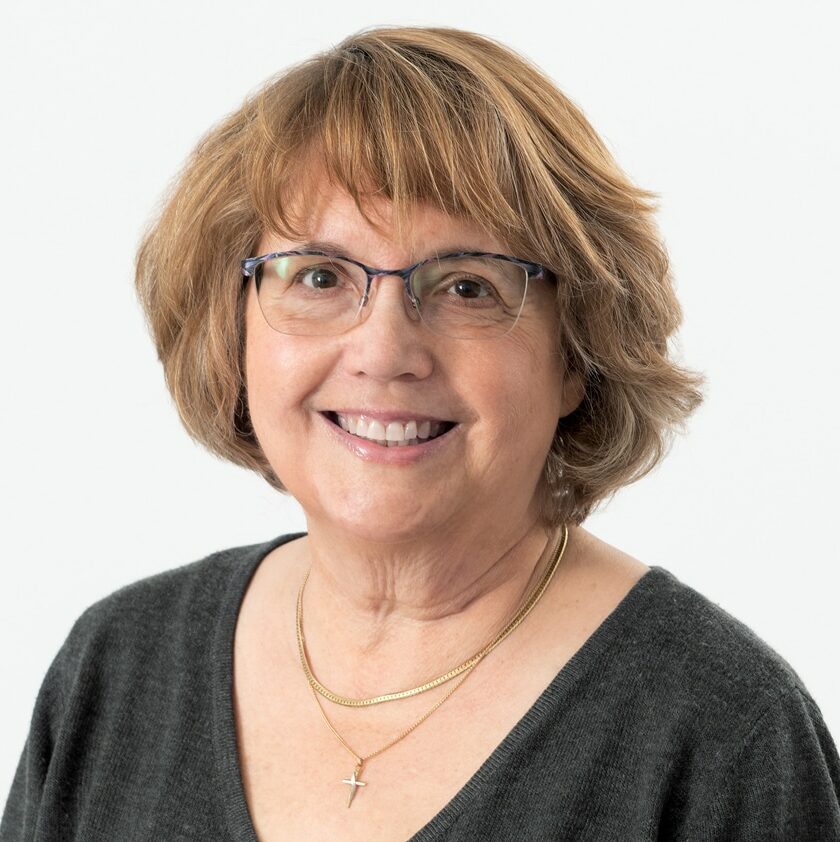
Kathy A. Bolten
Kathy A. Bolten is a senior staff writer at Business Record. She covers real estate and development, workforce development, education, banking and finance, and housing.